Spotlight on IKEA Supply
A misunderstood
industry: how Logistics
is rewriting the rules of work
Spotlight on IKEA Supply
A misunderstood
industry: how Logistics
is rewriting the rules of work
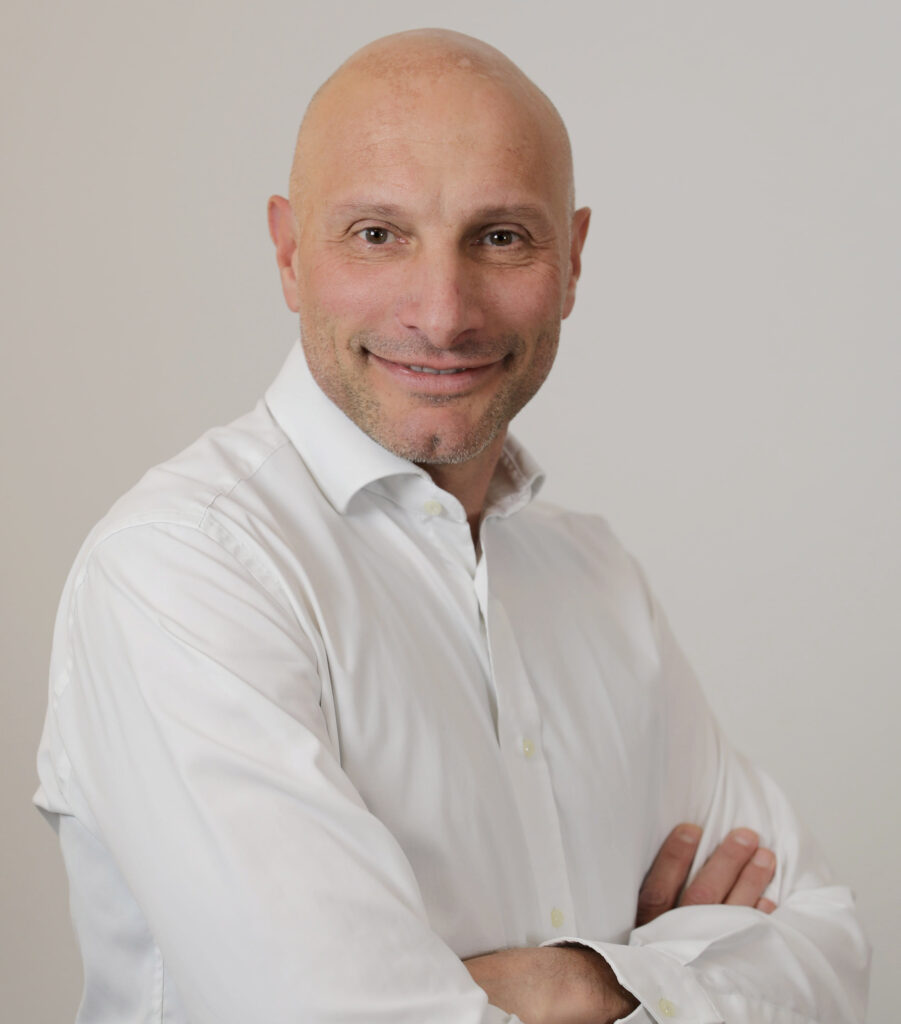
Interview with Andrea Colzani, Category Distribution Manager at IKEA Supply
We recently sat down with Andrea Colzani, Category Distribution Manager at Supply Chain Operations, IKEA Supply, in Inter IKEA Group, to discuss how logistics processes in his company are evolving. During this conversation, Andrea highlighted how new technologies, generational shifts and greater demands for work flexibility are making the industry more agile and inclusive.
Key Numbers from our Logistics 2023 Report
8.6 T$
Logistics current global value
9.9T$
predicted economic value by 2024
87%
of logistic workers are satisfied at work
40M
EVs will be sold annually in the next seven year
The Mechanisms of a Revolution
As with many industries during the past half-decade, logistics has moved through an intense period of transformation. You might even say it has been a revolution of sorts. The pandemic accelerated many systemic changes for the sector including adjustments to a more e-commerce dependent global economy. With several limitations on access to traditional logistics flows and shipping routes, industry leaders and managers had to get clever: new ways needed to be found to use technology to streamline processes and to find alternative suppliers for goods and product sourcing. All this change meant the industry also had to think about what kind of people and teams it needed to run future-facing operations with new remote and hybrid work structures.
Our business needed talent that could deliver greater flexibility in managing our teams, operations facilities and overall logistics systems, including enhanced means for inventory management. Plus, our growing need for greater overall sustainability began to drive our decisions on use of automation, robotics, green solutions for our warehouses and the geopolitical constraints for our supply chains”
An Exciting Time for Taking on Logistics Roles
Our 2022 Logistics Global HR Trends Report indicates that only 26% of respondents view logistics as a top industry to work in. Meanwhile, in that same research, people employed in the sector give generally high marks on their quality of life in the workplace (7.5 out of 10). There appears to be a misunderstanding of what work modernised logistics involves. Outdated tropes suggest that career paths in the industry revolve around driving trucks and loading boxes, with lots of low-paying manual labour and minimal chances of advancement. But the truth is that the sector constantly evolves: automation and machine integration have switched up the game, involving everything from data science-driven supply chain management to procurement planning and new automated and remote-run warehouse management systems (WMS) and warehouse control systems (WCS). Plus, given that customer service management, change management and similar tasks are now critically important to logistics businesses’ longevity, the industry increasingly focuses its hiring strategies on talent with top-level soft skills like communications, problem-solving or teamwork and collaboration.
Logistics careers can actually be well-paid and involve multiple career paths. With growing demand for greater technical knowledge, machine maintenance skills and insights into new technologies like AI and robotics, many companies offer on-the-job training and skills development programmes that help employees with career advancement. Moreover, with the increased adoption of automation and new technologies, employees have now access to hybrid work set-ups and flexible hours.”
The Push for Innovative Business Solutions
Sectoral transformation has also inspired and motivated teams at IKEA Supply to rethink how they structure and manage business operations with a look to the medium and longer term. The pandemic exacerbated the need to address structural challenges in business performance and this overall shake-up led the company to embark on important changes: pushing for rethinking of supplier relationships; setting higher ethical standards in procurement; and introducing strategy for human-machine collaboration in the use of electric vehicles (EVs) and autonomous vehicles (AVs) for warehouse operations, product delivery systems, and more. This brought about more efficient operations of scale, better managed task-planning, and more accurate and quicker order picking and product delivery.
A key benefit from our automated processes is improved accuracy in task completion. Automation makes operations more reliable and the technology layer on top of them ensures we have greater visibility into processes. We have real-time data on the movement of goods through the supply chain, and we are thus able to pinpoint and act on potential disruptions quickly and effectively.”
Constant Upksilling and Reskilling Efforts Ensure Logistics Work Remains Fresh and Exciting
There is never a dull moment in the tech-led world of modern logistics.
The industry’s growing use of automation, robotics and machine-driven processes means that the skills of its workforce must keep pace with innovation. Per our Logistics Global HR Trends Report, 69% of logistics workers plan on the need to reskill and engage in new training to ensure their future employability. This shows that there is a strong will inside the industry to adapt to a human-machine collaborative future.
New technologies, from working with robots in WMS on to new software platforms in WCS, inform what next-phase skills are needed and where businesses should offer extra training and reskilling support. Likewise, training efforts increasingly focus on mapping where does the business need its human talent most and where can machines take on redundant, mundane tasks. In warehouse systems, firms have worked toward greater integration of automated guided vehicles (AGVs) to free up their people teams for more complex loading processes and for maintenance and service roles. New talent is being hired to keep the machines running and for strategic planning of movement to achieve goals for operations efficiency, i.e., movement around warehouses with focused, minimal effort (routes) to keep energy costs down.
After taking the time to connect with a colleague who was not thriving in a team leader role, we found out he had a solid background in informatics. After 6 months, he became a WMS super user. Furthermore, the previous experience on the floor helped him to understand the dynamic and the logic of the daily work. Sometimes you just need to take an interest and ask the right questions.“
Moving Into a Soft Skills Approach
Industry experts have noted that there is a growing need for soft skills education when it comes to boosting their managers’ communication and leadership abilities and in their new hire evaluations.
Andrea Colzani confirms, “People talk a lot about technical and machine-related skills in logistics, but in recent years we have seen that investment in soft skills is just as critical for business success. We need talent with important leadership skills like the ability to negotiate and to listen to, and understand, colleagues and peers while having sufficient levels of empathy and kindness. It will likely come as a surprise to many candidates, and even employees, when I say that emotional intelligence (EQ) is something businesses like ours really value. We currently work across a lot of different technologies with teams that are on-site, remote and hybrid. This means we are better connected by not always truly connected. With more heavily tech-reliant roles, it can be difficult to build a company culture and to form between-employee bonds and relationships. That’s why we invest time into helping workers understand how they can communicate better.“
In conclusion, it is clear that the logistics industry is continuing to forge a way forward in a challenging period of transition. But companies like IKEA Supply are embracing these challenges and exploring new possibilities for making human-machine collaboration work, particularly at a time when many employees are concerned about an unknown future with their robot counterparts. Now it is incumbent upon logistics managers and their HR teams to make the skills evolution as seamless as possible, so that the industry can boost its reputation as a career destination for innovators, strategists, and challenge-seekers.
About IKEA Supply
IKEA unites thousands of co-workers and hundreds of companies with different owners, all over the world, organised in a franchise system.
The IKEA franchise system is a network of different companies operating under the IKEA brand.
It consists of IKEA franchisees, Range, Supply, Communications, as we call INTER IKEA GROUP.
And it consists of the IKEA franchisor, the retailers.
In IKEA Supply, we find Supply Chain Operations.
Supply Chain Operations is a trusted leader, setting industrial standards for seamless planning and execution of IKEA goods flow, connecting stakeholders and partners worldwide.
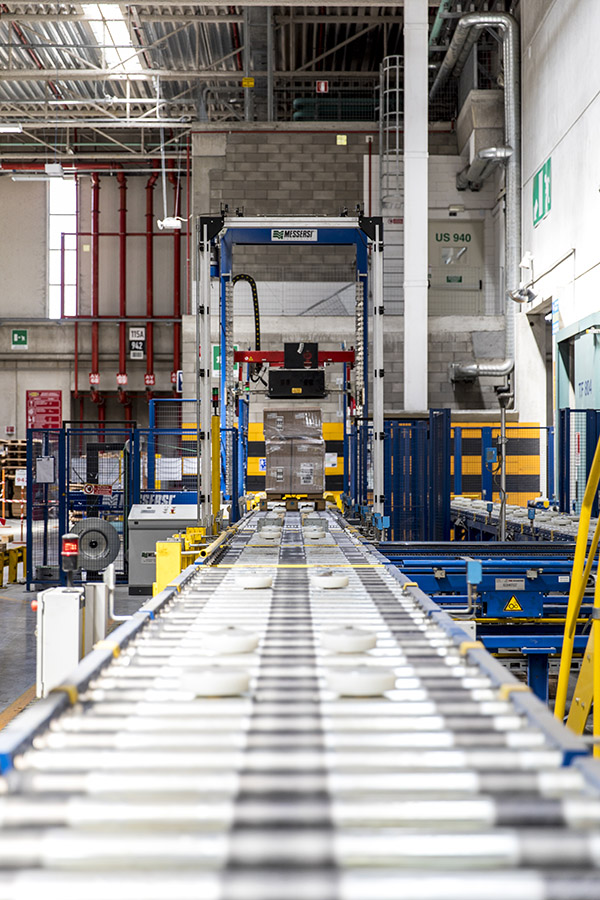
Fill the form to get in touch with an expert.